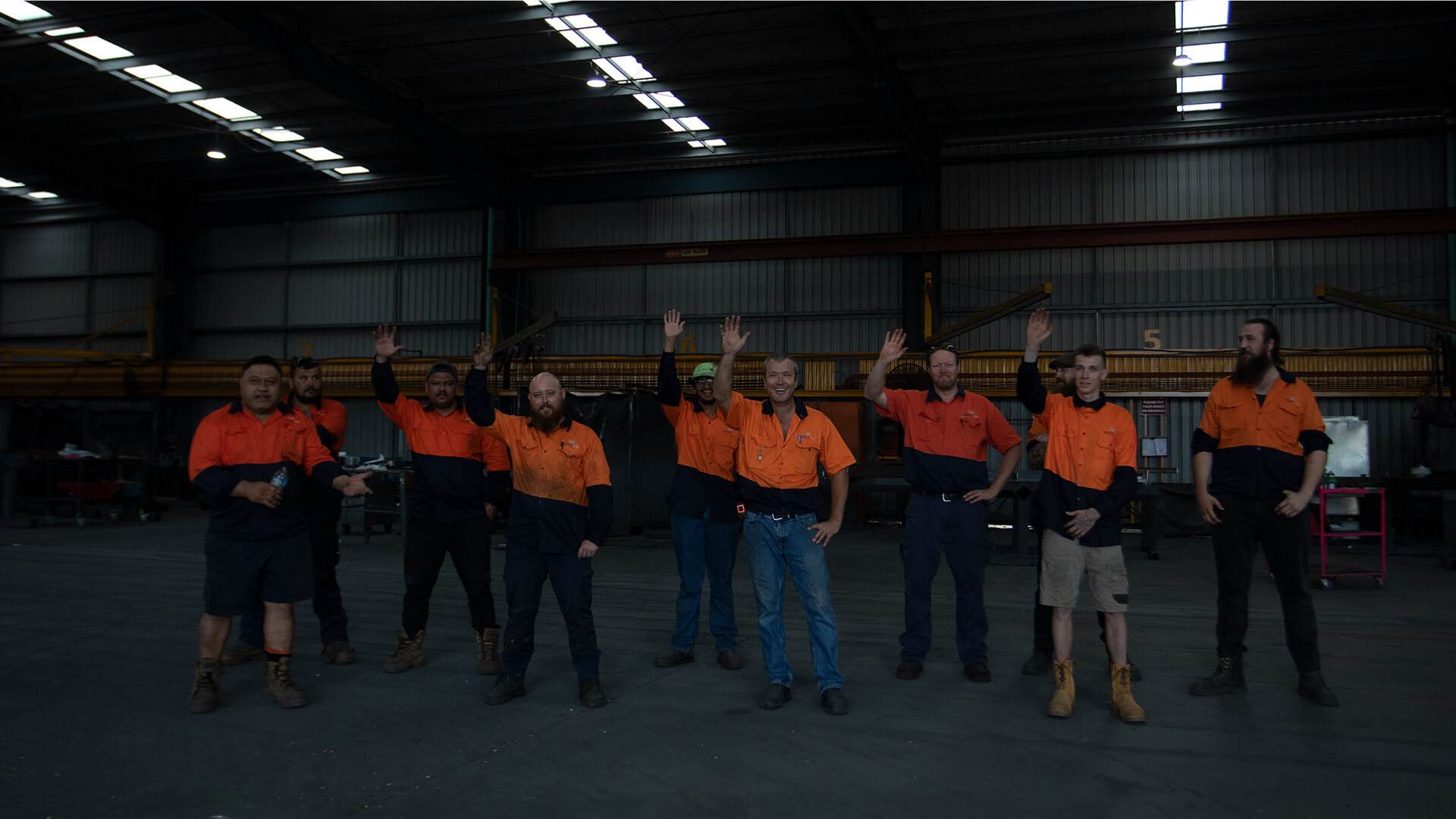
Project Showcase
FAQs
Steel is essentially an element of iron that has been processed to control the amount of carbon in the material. While iron melts at around 1510 degrees Celsius, steel typically melts at about 1370 degrees Celsius. The exact melting point of steel, however, will depend on the specific type of steel being referred to. Most steel is composed of a number of other metals, each of which has an effect on its strength, resistance to corrosion and the ease with which it can be fabricated. These metals will also affect its melting point.
Steel fabrication refers to the formation of metal structures through the processes of cutting, bending and assembling structural steel. During the cutting process, steel is cut in one of three methods: shearing, chiselling or sawing; torching; and numerical control cutters. The bending process is carried out by either hammering or press brakes. With modern technology and software, this process can be done seamlessly. The assembling stage can be done by means of a number of methods, including welding, riveting and threaded fasteners.
The cost of our steel fabrication services will depend on the size of your particular project. If you would like to find out exactly what you can expect in terms of costs, we recommend that you request a quote from us. To do so, we ask that you simply complete our online form and our team will get back to you within two working days. The more details you can give us in terms of your project, site, location and plans, the better we can do at giving you an accurate quote. Alternatively, you are welcome to set up a meeting with us to discuss your project.
Structural steel is made from a combination of iron and carbon, as well as some other components like manganese, which improve its strength and durability. In fact, manganese is one of the most commonly added ingredients to structural steel (after iron and carbon) because it helps to bind the elements of the material to avoid cracking when it is being processed. Phosphorus is also sometimes added to structural steel as it helps to improve the strength of the material. Other possible additives include silicon, tungsten, vanadium, and chromium.
A PFC steel beam, also known as a steel channel, is used in a number of industries, including residential and commercial construction. PFC stands for Parallel Flange Channel, and these types of beams are made from very versatile steel that can be used as both horizontal and vertical supports. PFC steel beams can be also be used in the construction of columns, as support beams above doors, as well as supporting beams in floors. These steel beams are available in a wide range of widths and depths, depending on the intended use.
The first step in making structural steel is to crush and sort raw iron. Through a series of refining processes, the best grades of iron are gathered. Ore is then heated in order to remove any impurities. During the heating process, the pure iron sinks and the molten iron is drawn off and heated further. Other components are then added to enhance the strength and machinability of the material. The main ingredients in structural steel are iron and carbon, while manganese is also often added. Generally, the more carbon there is in the mixture, the greater the strength of the final steel.