Frequently Asked Questions
3D scanning is a technology that captures precise measurements of physical objects or environments using lasers or cameras. For structural steel projects, it offers benefits such as:
- Precision: Accurate measurements ensure precise fabrication and construction.
- Efficiency: Facilitates detailed planning, design, and clash detection, reducing errors and project timelines.
- Cost Savings: Minimises rework and site visits, leading to lower project costs.
- Enhanced Collaboration: Improves communication among stakeholders with clear, visual project data.
Overall, 3D scanning enhances project accuracy, efficiency, and collaboration in structural steel fabrication and construction.
3D scanning offers significant advantages over traditional methods in structural steel fabrication. It enhances accuracy by providing precise measurements and detailed data capture, reducing errors that commonly occur with manual methods. The technology speeds up the process by efficiently capturing comprehensive site information in a single scan, minimising the need for multiple visits and manual measurements. This capability is particularly beneficial for handling complex geometries and existing structures, allowing for accurate modelling and clash detection early in the project timeline. The detailed 3D models generated facilitate better visualisation and planning, improving decision-making throughout the fabrication and construction phases. Additionally, 3D scanning produces thorough as-built documentation that supports future renovations, maintenance, and compliance needs, ultimately leading to cost savings and streamlined project timelines.
3D scanning contributes to cost savings and project timelines in several key ways. Firstly, it reduces the need for repeated site visits and manual measurements by capturing comprehensive data in a single scan, minimising labour hours and travel costs. This efficiency accelerates the initial data collection phase, allowing design and fabrication processes to commence sooner. By providing accurate measurements and detailed 3D models early in the project, 3D scanning helps identify potential clashes and design issues upfront, preventing costly rework during construction. The precise data also supports more accurate material estimates and reduces material waste. Overall, these factors combine to streamline project workflows, optimise resource allocation, and shorten overall project durations, resulting in significant cost savings and improved project timelines.
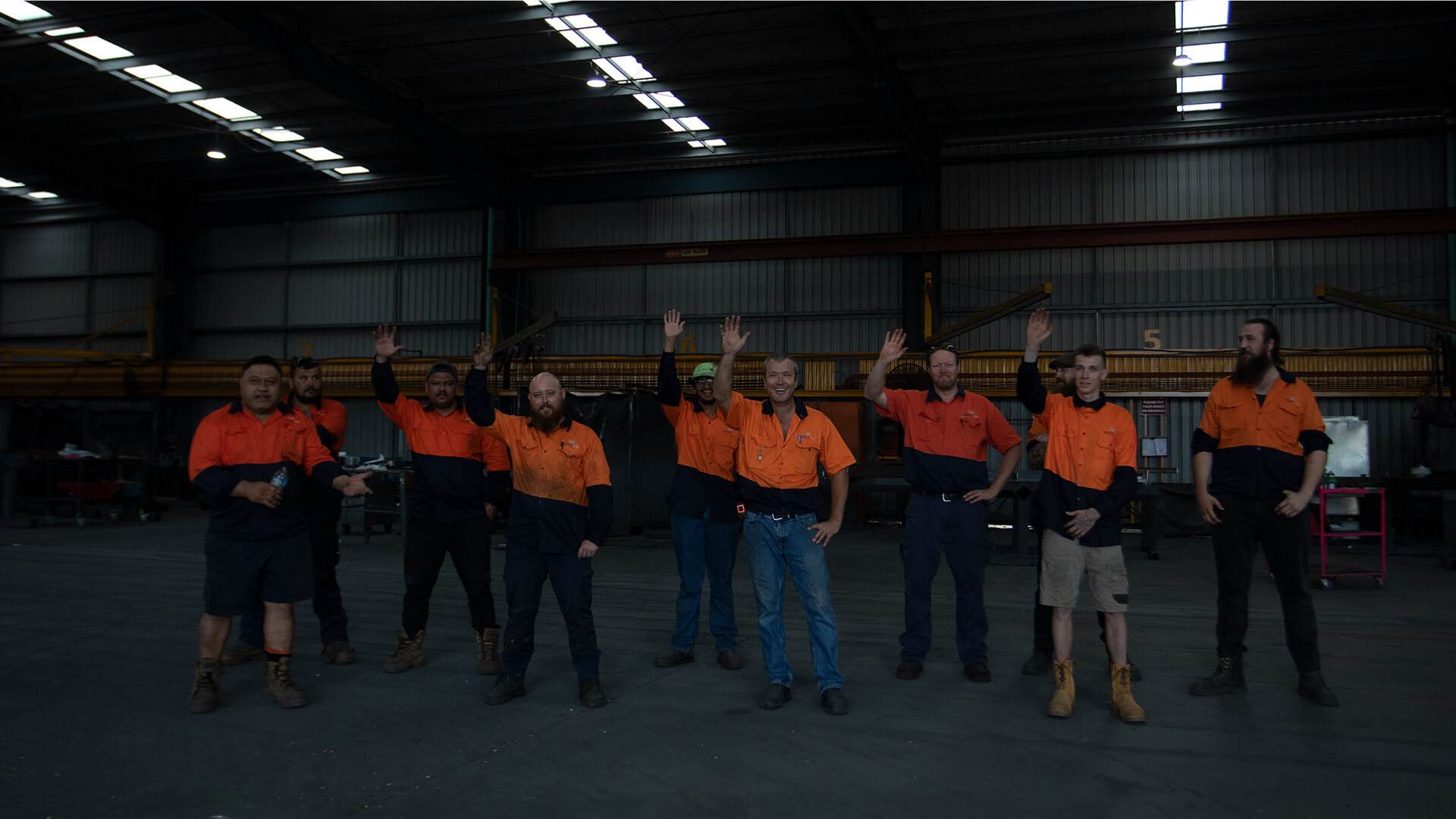
Project Showcase
What does this mean for large construction projects?
Traditionally, a draftsperson or site engineer would be required to take manual measurements to draw-up a design layout which would then be used to determine required materials.
As any project manager would understand too well, these measurements and plans are open to human error often causing issues within the supply chain.
Contemporary steel industry innovators are now able to use advanced scanning and digital imaging technology to take a 3D snapshot of the site. This information is used by a draftsperson who then creates a complete digital representation of the worksite.
The data and information are fed to the new machinery, which cuts and processes a precise amount of material ready for transportation back to the site.
Traditionally, a small mistake in measurement could potentially cause a range of issues:
- Extending completion dates
- Blowing budgets
- Over or underestimating required materials
With new technology and machinery, human error is completely removed from the equation.
Contact BridgeFab for structural steel projects
At BridgeFab we can take care of the structural steel process from start to finish – so contact us today or call on (07) 3373 8777.